Empowering sustainable energy production with IoT and Digital Twin.
About the company
Methaplanet sets itself apart in the realm of biomass pellet innovation by seamlessly merging energy conservation with efficiency, all within the framework of a circular economy.
Through their top-of-the-line pellet mills and factories, they are a leading player in the industry, providing solutions that are both environmentally friendly and cost-effective.
The challenge
Navigating Production Pitfalls
Methaplanet grappled with production inefficiencies, hurdles in real-time equipment and process oversight, and a diminished clarity on the comprehensive performance of their production assembly.
The approach
Strategizing for efficiency
Our strategic approach was to synergize cutting-edge technology with their production process. The intent was to provide a blend of real-time monitoring and virtual simulations, optimizing immediate/long-term operations.
-
Discovery - Identify challenge
- IoT integration
-
Process - Implement digital twin
- Platform development
-
Outcome - Real-time data
- High performance
The solution
Future-proofing production: A leap with IoT and simulations
For Methaplanet, staying ahead of curve meant embracing cutting-edge technology. We initiated this transformation by integrating an IoT Gateway. This gateway became the eyes and ears on the production floor, observing, alerting, and allowing for proactive interventions.
Taking it a step further, we introduced Methaplanet to Digital Twin – a virtual playground where they could experiment, learn, and innovate without tangible risks. By simulating real-world scenarios, they could pinpoint optimization strategies, ensuring the real-world application was nothing short of perfection.
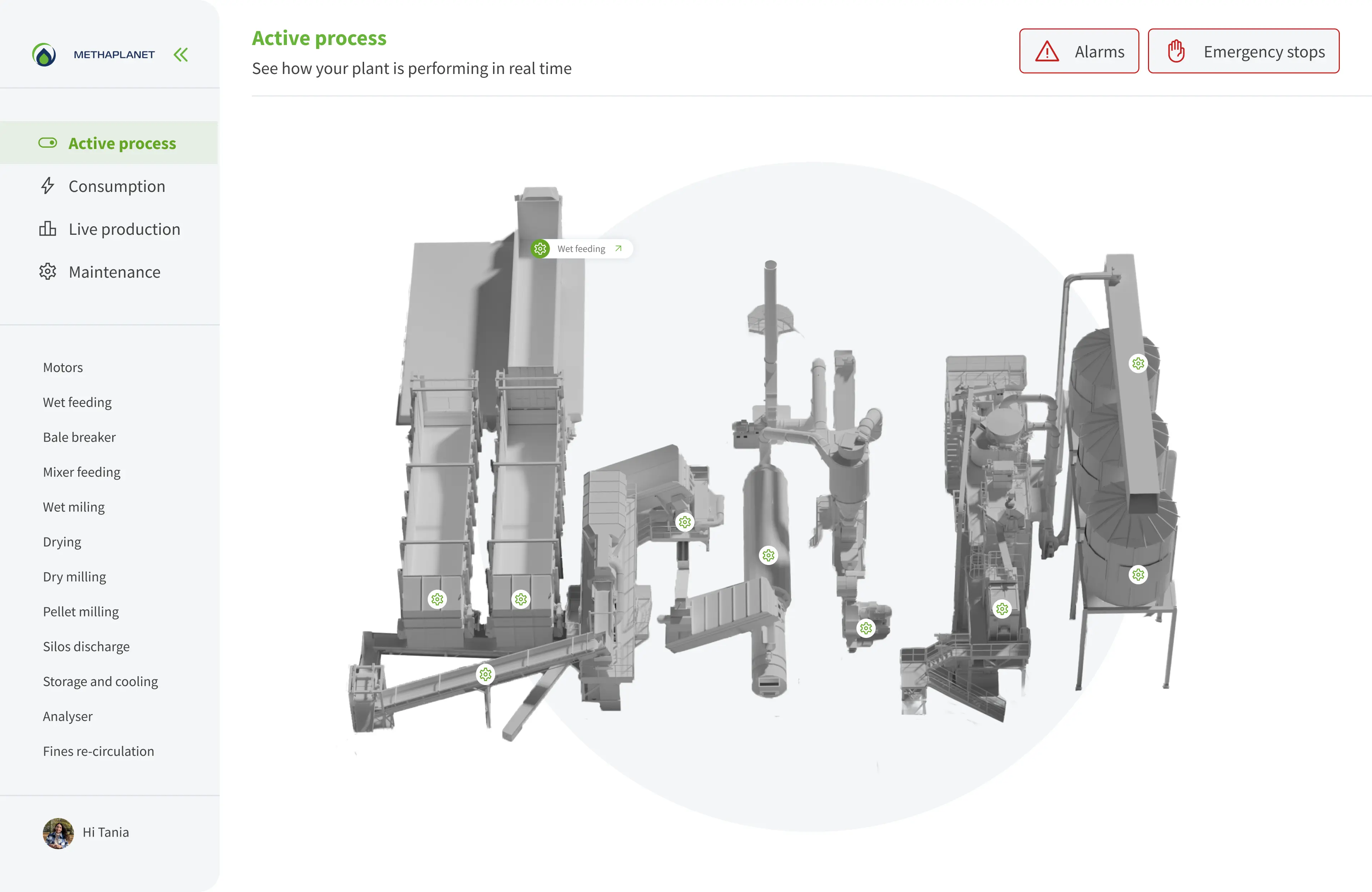
The results
Efficiency unleashed
Through the vigilant eyes of the IoT Gateway, real-time monitoring pinpointed production hiccups. The result? Immediate interventions, drastic reductions in inefficiencies, and a smoother, faster production line.
Optimized production flow
The data harvest from our IoT Gateway shed light on latent improvement areas. Armed with this insight, Methaplanet could make strategic shifts, supercharging their production performance.
Savings galore
With our IoT system in place, potential equipment troubles didn't stand a chance. Predictive maintenance preempted major breakdowns, curtailing both downtime and hefty repair bills.
Precision perfected
The Digital Twin wasn't just a mirror but a magnifying glass. By simulating assets and processes, Methaplanet could dive deep, fine-tuning their operations for optimal outcomes.
-
00. Troviq: A new brand identity and website design for Troviq Private Markets
Netherlands
-
01. Empowering Enterprises: Joine Technologies' seamless transition to a next-gen B2B payment platform
Netherlands
-
02. GarDsign's Evolution: Pivoting from a PHP Legacy System to Java Microservices
Netherlands